Forschungsschwerpunkte
Die Arbeitsgruppe Albert forscht an der Substitution fossiler Basischemikalien durch nachwachsende Rohstoffe. In Zusammenarbeit mit industriellen und akademischen Partnern wird an alternativen Energiequellen und Chemiegrundstoffen gearbeitet, um eine nachhaltige, biobasierte Grundlage für die zukünftige industrielle Entwicklung zu schaffen.
Katalytische Wertschöpfung aus Biomasse - Teamleitung Jan Krueger
Die chemische Industrie der Zukunft muss sich von der Nutzung fossiler Rohstoffe wie Kohle, Erdöl und Gas hin zu nachhaltigeren organischen Ressourcen bewegen. Unter den erneuerbaren Energiequellen bietet Biomasse ein großes Substitutionspotenzial. Daher wächst in den letzten Jahren das Interesse an kostengünstigen Biomasse-Umwandlungsverfahren zur Herstellung wertvoller Plattformchemikalien.
Lignozellulosehaltige Biomasse ist die am häufigsten vorkommende Klasse biogener Materialien und enthält typischerweise mehr als 50 Gewichtsprozent Zucker, die zu wertvollen Plattformchemikalien aufgewertet werden können. Lignozellulose besteht hauptsächlich aus drei Komponenten: Zellulose (ca. 50 %), Hemizellulose (25–30 %) und Lignin (15–25 %). Das aromatische Lignin ist der bisher am wenigsten genutzte Bestandteil. In der Zellstoff- und Papierindustrie wurde es traditionell aufgrund seines hohen Heizwertes zur Erzeugung von Wärme und Strom durch Verbrennung eingesetzt. Es bietet jedoch großes Potenzial zur Herstellung hochwertiger Chemikalien wie Vanillin und dessen Derivate. Hemizellulose enthält hauptsächlich C5-Zucker wie Xylose oder Arabinose, die wichtige Anwendungen bei der Herstellung von Biokraftstoffen (z. B. Bioethanol) und bei der Erzeugung wertvoller chemischer Zwischenprodukte (z. B. Furfural) finden. Zellulose gilt als eines der am häufigsten vorkommenden Biopolymere der Erde und besteht aus linearen β(1,4)-verknüpften Glukoseketten (C6). Diese können in wertvolle Produkte wie Biokraftstoffe und Plattformchemikalien wie Ameisensäure, Levulinsäure oder Milchsäure sowie daraus abgeleitete Produkte, z. B. verschiedene Oxygenate, umgewandelt werden.
Bei der Verarbeitung von Monosacchariden und deren Derivaten, die aus Zellulose gewonnen werden, entstehen gleichzeitig dunkel gefärbte Feststoffe, sogenannte Humine. Diese sind in nahezu allen Lösungsmitteln unlöslich, außer in konzentrierter Natronlauge, und verursachen mehrere Probleme bei der Biomasseverarbeitung. Laut Literatur bestehen die grundlegenden Bausteine der Humine höchstwahrscheinlich aus Furanringen, die durch verschiedene aliphatische funktionelle Gruppen verbunden sind. Diese Furanringe können bis zu 60 % der Huminstruktur ausmachen, während die aliphatischen Verbindungen etwa 20 % ausmachen. Die Verwertung von Huminen bietet großes Potenzial für eine kosteneffiziente Herstellung von Plattformchemikalien wie Maleinsäure.
Algenbiomasse ist eine reichlich vorhandene erneuerbare Quelle für Kohlenstoff (C) und Stickstoff (N), die in einer einzigen Spezies kombiniert vorkommen. Besonders Makroalgen stellen eine große und bisher wenig genutzte Ressource für die Proteinextraktion dar, mit Vorteilen wie schnellen Wachstumsraten und einer geringen Umweltbelastung. In jüngerer Zeit haben Makroalgenproteine in der wissenschaftlichen Forschung starkes Interesse für Anwendungen in nicht-lebensmittelbezogenen Branchen wie der Kosmetik- und Pharmaindustrie geweckt.
Ansprechpartner: Jan Krueger, M.Sc. (jan-dominik.krueger"AT"uni-hamburg.de)
Chemische Energiespeicherung (Power-to-X) - Teamleitung Nick Herrmann
Mit überschüssigem Strom aus erneuerbaren Energien wie Photovoltaik und Windkraft kann Wasserstoff durch Elektrolyse nachhaltig produziert werden. Aufgrund der geringen volumetrischen Energiedichte von Wasserstoff ist die technische Speicherung durch Verdichtung und Verflüssigung mit großem Aufwand, speziellen Materialien und hohen Kosten verbunden. Insbesondere die Langzeitspeicherung großer Mengen an Wasserstoff ist schwierig und kostenintensiv.
Alternativ kann der regenerativ gewonnene Wasserstoff in einem Power-to-X-Verfahren einer weiteren Wertschöpfung zugeführt werden. Mit CO2 aus Kraftwerken, Industrieabgasen und Biogasanlagen können Basischemikalien und Kraftstoffe hergestellt werden. Die Herstellung von z. B. Methan, Methanol, Dimethylether oder Olefinen unter konstanten Reaktionsbedingungen ist erprobt, berücksichtigt jedoch keine fluktuierende Wasserstoffbereitstellung aus erneuerbaren Energien.
Aufgrund dieser dynamischen Rahmenbedingungen müssen neuartige, flexible und robuste Katalysatoren entwickelt werden, um unerwünschte Nebenreaktionen und Katalysatordeaktivierung zu minimieren. Zur prozesstechnischen Evaluierung werden die Katalysatoren in einer stufenlos-regelbaren Festbettanlage mit fluktuierenden Stoffströmen und Temperaturen reaktionstechnisch untersucht.
Die Wahl der optimalen Kombination aus Aktivkomponente und Trägermaterial des Katalysators sowie dessen Morphologie ist neben den Reaktionsbedingungen maßgeblich entscheidend für die katalytische Performance. Hierzu werden vielversprechende Power-to-X Anwendungen wie die (Reverse) Wasser-Gas-Shift-Reaktion, die CO2- Methanisierung sowie die Methanol- und Dimethylethersynthese aus CO2 unter dynamischen Reaktionsbedingungen untersucht. Diese sind über thermodynamische Gleichgewichte miteinander gekoppelt, sodass Nebenprodukte zwangsläufig entstehen. Ziel der Forschung ist es, mit einem selektiven und robusten Katalysator die jeweils optimalen Reaktionsparameter zu bestimmen, um die Ausbeute der gewünschten Verbindung unter fluktuierenden Reaktionsbedingungen zu maximieren.
Ansprechpartner: Nick Herrmann
E-Mail: nick.herrmann"AT"uni-hamburg.de
Nanomaterialien für die Katalyse - Teamleitung Dr. Maximilian Poller
Katalysatoren spielen eine zentrale Rolle in der modernen Chemie, da sie die Aktivierungsenergie von Reaktionen senken und so effizientere, energiesparende Prozesse ermöglichen. Im Zuge einer nachhaltigen Entwicklung ist ihre Bedeutung für die Transformation der chemischen Industrie wichtiger denn je.
Unsere Forschung unterstützt den Wandel von fossilen Ausgangsstoffen hin zu nachhaltigen Rohstoffen wie grünem Wasserstoff, Kohlendioxid (CO₂) und Biomasse. Dieser Übergang bedeutet einen grundlegenden Paradigmenwechsel: Statt Plattformchemikalien aus einfachen Kohlenwasserstoffen aufzubauen, gilt es nun, die gezielte Zerlegung hochfunktionalisierter Moleküle aus Biomasse zu steuern. Während konventionelle Prozesse meist oxidativ ablaufen, erfordern nachhaltige Alternativen – insbesondere im Umgang mit CO₂ und grünem Wasserstoff – vermehrt reduktive Reaktionen.
Die Entwicklung neuer Katalysatormaterialien ist daher unerlässlich für diese zukunftsweisenden chemischen Prozesse. In unserem Team konzentrieren wir uns auf das Design, die Synthese und die umfassende Charakterisierung innovativer Katalysatoren, die effizient, selektiv und aus reichlich vorhandenen, ungiftigen Elementen hergestellt sind.
Mit unserer Arbeit möchten wir eine umweltfreundlichere chemische Produktion ermöglichen und den Wandel der chemischen Industrie hin zu mehr Nachhaltigkeit aktiv mitgestalten.
Wenn Sie mehr über unsere Forschung erfahren oder mit uns zusammenarbeiten möchten, wenden Sie sich gerne an Dr. Maximilian J. Poller und das Katalysatorentwicklungs-Team.
Maßstabsvergrößerung und Miniplanttechnik - Teamleitung Dr.-Ing. Dorothea Voß
Im Zuge der Entwicklung eines chemischen Prozesses bis hin zur Industriereife spielt die Maßstabsvergrößerung eine entscheidende Rolle. Hierbei bildet die Technische Chemie das Bindeglied zwischen der Chemie und der Verfahrenstechnik. Zunächst werden neue Synthesestrategien im Labor entwickelt (Chemie) und anschließend erfolgt die sichere Übertragung der im Labor gefundenen chemischen Umsetzung in den technischen Maßstab (Verfahrenstechnik).
Die Miniplant-Technik bildet die Grundlage der Maßstabsvergrößerung. Bei einer Miniplant handelt es sich um eine Kleinanlage im Labor- oder Technikumsmaßstab mit einem Durchsatz von 0,1-1 kg h-1. Aufbauend auf diskontinuierlichen Laborversuchen, in denen unterschiedliche Einflussparameter wie Druck, Temperatur oder Katalysatorsysteme untersucht werden, können in einer Miniplant erstmals kontinuierliche Untersuchungen durchgeführt werden. Mit Hilfe der Miniplant können Machbarkeitsstudien durchgeführt und Kreisläufe sowie Rückführungen überprüft werden. Auch die Wechselwirkungen zwischen den Prozesseinheiten können untersucht und das dynamische Verhalten sowie An- und Abfahrverhalten überprüft werden. Zudem können erste Studien zu Langzeiteffekten durchgeführt werden. Insgesamt stellt die Miniplant also ein Abbild des späteren technischen Prozesses dar. Vorteilhaft ist dabei, dass in Miniplants standardisierte Laborgeräte (wie z.B. Wärmetauscher, Pumpen und Reaktoren) zum Einsatz kommen. Dadurch sind Miniplants platzsparender, flexibler und kostengünstiger als klassische Pilotanlagen. Zusätzlich sind apparative Umbauten relativ schnell durchzuführen.
Bei der Maßstabsvergrößerung ist die Auslegung der chemischen Reaktoren im Hinblick auf Form, Größe und Betriebsweise genauso wichtig wie die Auslegung der Trennkonzepte für die geforderte Produktionsmenge. Ziel ist hierbei stets ein möglichst großer Scale-Up Faktor zur Einsparung von Entwicklungszeit und der Kosten. Das in der Miniplant entwickelte Verfahrenskonzept sowie die erzeugten Versuchsergebnisse stellen die Grundlage für ein sicheres Scale-up in den technischen Maßstab dar.
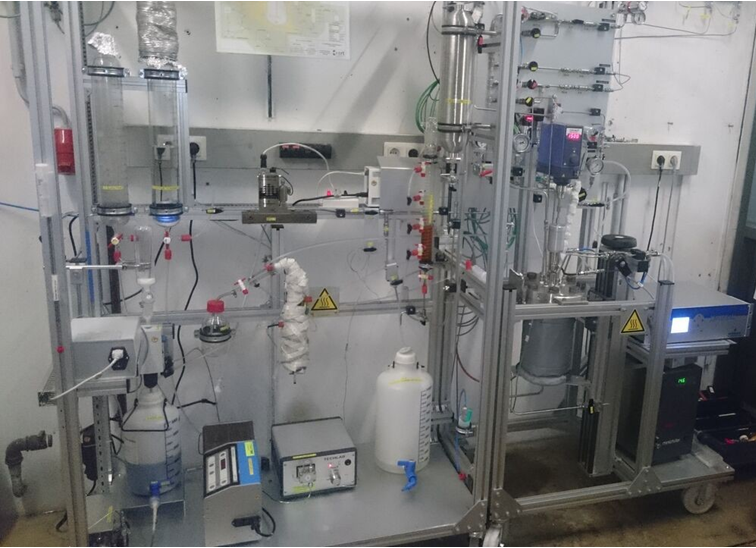
In unserer Arbeitsgruppe beschäftigen wir uns mit der Maßstabsvergrößerung verschiedener Prozesse. Bei der Mehrheit unserer Projekte wird nach der Optimierung des Systems eine Maßstabsvergrößerung vorgenommen und eine Durchführung der Prozesse in einer Miniplant angestrebt. Hierbei führen wir alle Schritte von der Konzeptionierung, dem Aufbau und der Inbetriebnahme der Miniplants selbst durch und erarbeiten ebenfalls die benötigten Sicherheitskonzepte für den sicheren Betrieb der Miniplants.
Ansprechpartnerin: Dr.-Ing. Dorothea Voß (dorothea.voss"AT"uni-hamburg.de)