Reaction plants
The manufacturing process influences the properties of polymers. Understanding the course of the reaction is essential for process development. That is why the reactor systems used are equipped with online monitoring. Furthermore, new reactor concepts are being researched.
The design of new reactor types is actively supported by our in-house precision mechanical and glass-technical workshops.
Reaktoranlagen
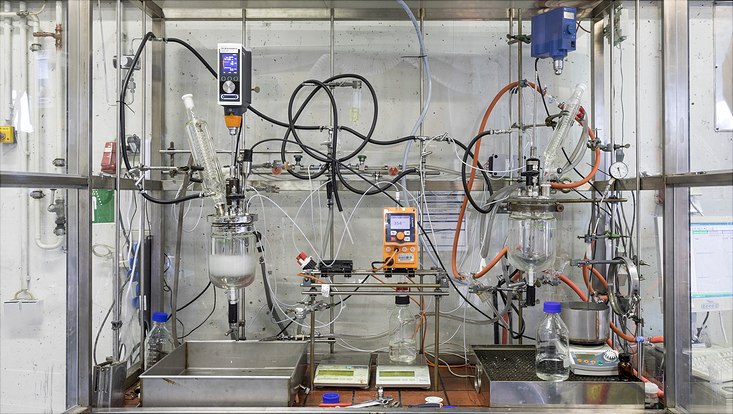
Photo: UHH/Mentz
Polymerization plant
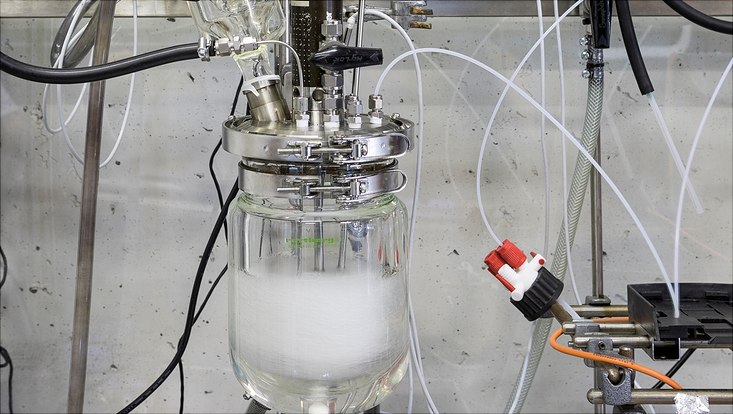
Photo: UHH/Mentz
Glass reactor with dosing and reaction monitoring setup.
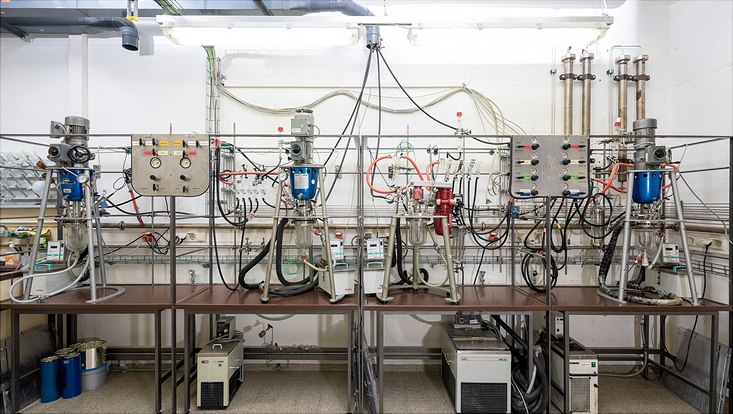
Photo: UHH/Mentz
Glass reactors for catalyst screening.
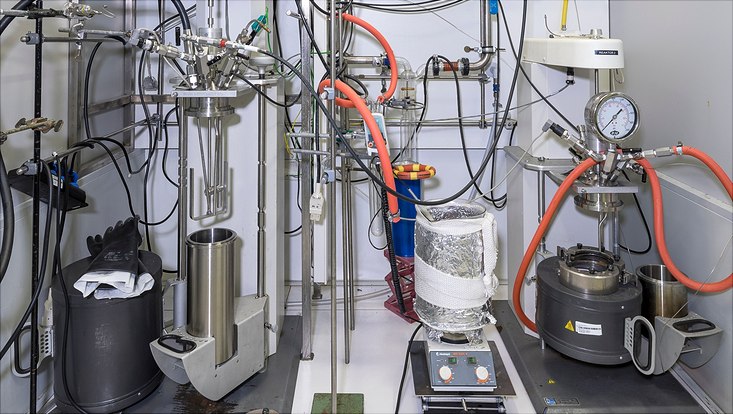
Photo: UHH/Mentz
2 l high-pressure vessel for the synthesis of CO2-based polymers.
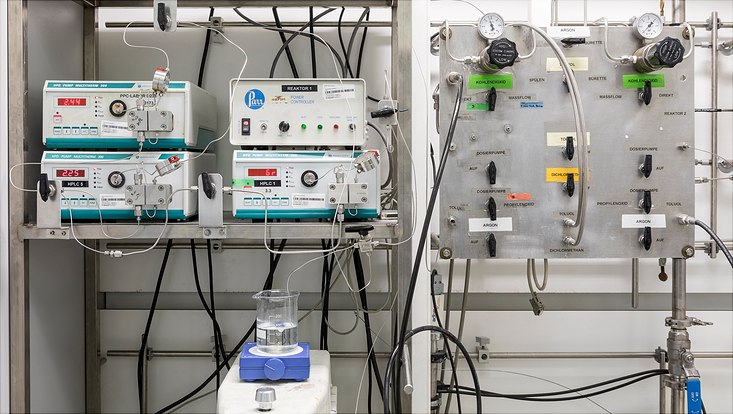
Photo: UHH/Mentz
Dosing system for high-pressure vessels.
Polymerization plants
The performance of polyreactions often requires the use of stirred tanks and autoclaves to handle higher viscosities, pressures and temperatures. We use glass and stainless steel reactors from laboratory to pilot plant scale. In addition to the stirring vessels, the polyreaction plants are often equipped with a complex infrastructure, such as a computer-controlled process control system with online reaction tracking and dosing systems. Suitable systems are available for almost every technical issue. If that should, for once, not be the case, novel reactor concepts are developed that can be quickly tested using rapid prototyping (3D printing).
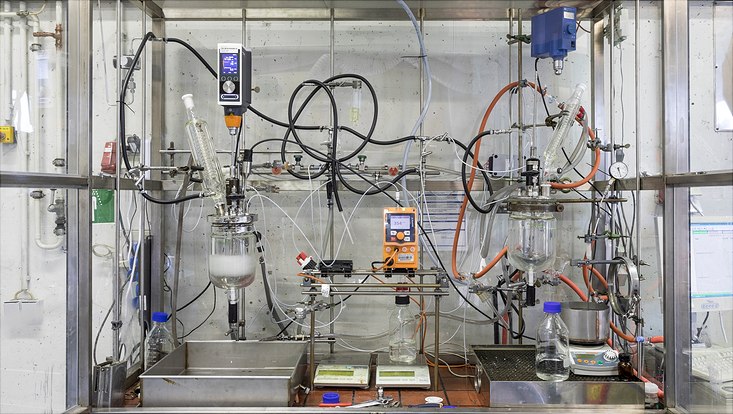
The performance of polyreactions often requires the use of stirred tanks and autoclaves to handle higher viscosities, pressures and temperatures. We use glass and stainless steel reactors from laboratory to pilot plant scale. In addition to the stirring vessels, the polyreaction plants are often equipped with a complex infrastructure, such as a computer-controlled process control system with online reaction tracking and dosing systems. Suitable systems are available for almost every technical issue. If that should, for once, not be the case, novel reactor concepts are developed that can be quickly tested using rapid prototyping (3D printing).
Foto: UHH/Mentz
Pressure reactors
Pressure reactors are available for the homo- and copolymerization of ethene, propene, α-olefins, and butadiene using the low-pressure process up to 5 bar. The polymerization process and the catalysts are examined in 1 L screening reactors (glass or stainless steel) to map the parameter space. For full characterization of the polymeric materials produced, the scale-up was realized on a kg scale.
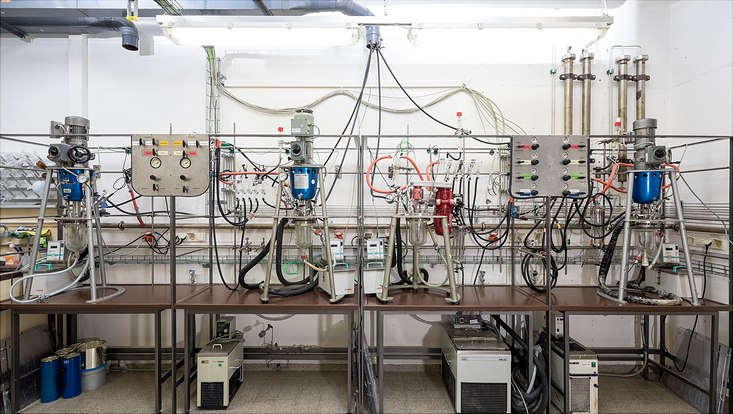
All reactions can be carried out under an inert gas atmosphere. Additional glove boxes are available for the synthesis of air- and moisture-sensitive substances.
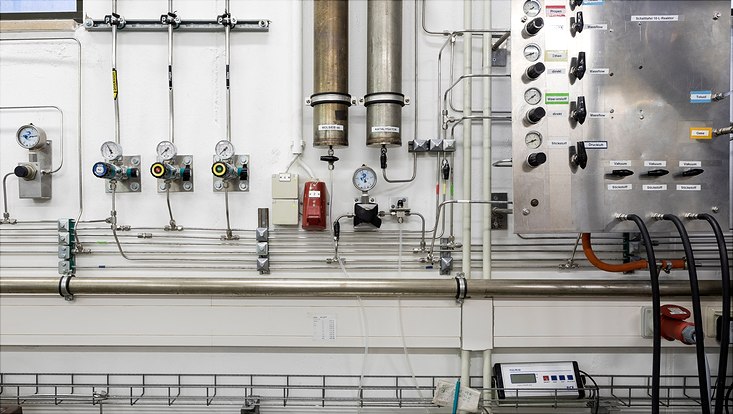
High-pressure reactors (up to 200 bar)
Processes with pressures up to 200 bar can be run using the high-pressure polymerization plant. For this purpose, stainless steel reactors from 300 mL to 2 L are available, which are equipped with an extensive process control system. These reactors are used, for example, for the copolymerization of CO2 with epoxides.
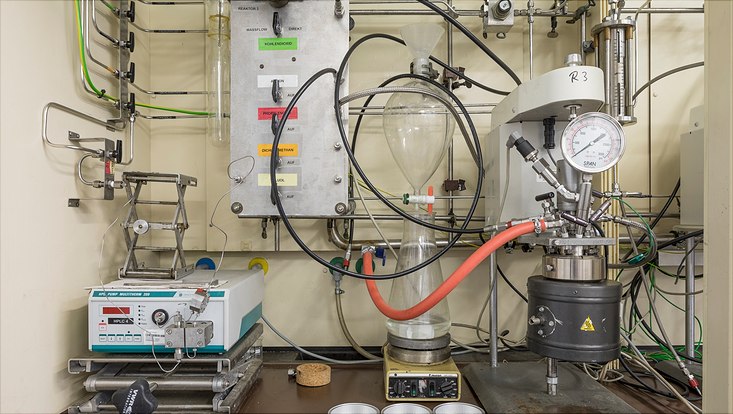
Scale-Up
The polycondensation places high demands on the reaction procedure and the reaction plant. At the institute, the production and the associated down streaming of polyesters and polyamides by means of polycondensation was gradually transferred from the laboratory scale to the kg scale (10 L stainless steel reactor).
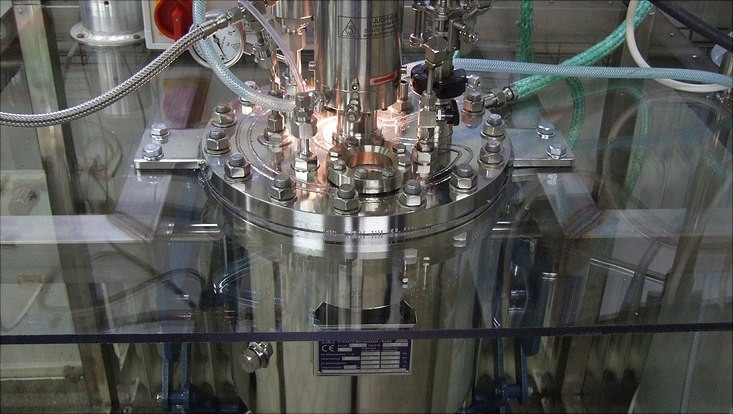
A 10 L stainless steel pressure reactor is available for the production of polyolefins, and a mini-plant is under construction. The mini-plant technology enables the small-scale development of process engineering productions from the laboratory to a large-scale plant without the detour via a test plant. It contains a 50 L pressure reactor, in which polyolefins, polyethers, and polycarbonates are to be manufactured, starting from spring 2020.
Reaction calorimetry
Isoperiboles and isothermal reaction calorimetry
Reaction calorimetry is generally used to determine the thermal energy that occurs during chemical reactions. In contrast to other physical parameters, this cannot be measured directly but requires suitable devices to determine the occurrence of heat flows over time. The aim of most investigations is usually the determination of reaction enthalpy and possibly kinetics, which are not only essential in science, but also for the design of large-scale plants.
Two Mettler Toledo reaction calorimeters are operated here, an RC1e high temp and an RC1 classic. For both calorimeters together, there are currently four dosage sections for semi-batch operation. The more recent version of the device is located in a laboratory fume hood so that it is possible to work also with harmful substances. The reactors used are the Mettler MP10 (glass up to 10 bar, without floor outlet) and the Mettler HP60 (stainless steel up to 60 bar pressure, with floor outlet).
As a self-developed extension, the commercial calorimeters have been upgraded to heat balance calorimeters: by means of two temperature sensors at the inlet and outlet of the heat transfer oil of the jacket circuit and separate high-resolution measuring equipment, the jacket circuit serves as a second balance room. In offline mode, the often problematic term U - A can be precisely determined in heat flow calorimetry.
Spray drying and levitation
Spray drying and levitation
Spray towers are used to produce fine powders by drying a droplet mist in a hot gas stream. The method of spray drying can also be used to dry temperature-sensitive substances since the relatively high droplet surface causes effective cooling by evaporating the solvent. Depending on the desired products, parameters, such as air humidity, temperature, flow rate, droplet size or concentrations can be varied.
An extension of spray drying is reactive spray drying – spray polymerization. The chemical reaction takes place during drying and shaping so that three essential steps in product formation take place in one production step. The crucial challenge is to optimize the interrelated processes by appropriate process control. Thus, in the case of solids, for example, early drying prevents the reaction from progressing, whereas drying too late leads to agglomeration of the particles at the end of the tower.
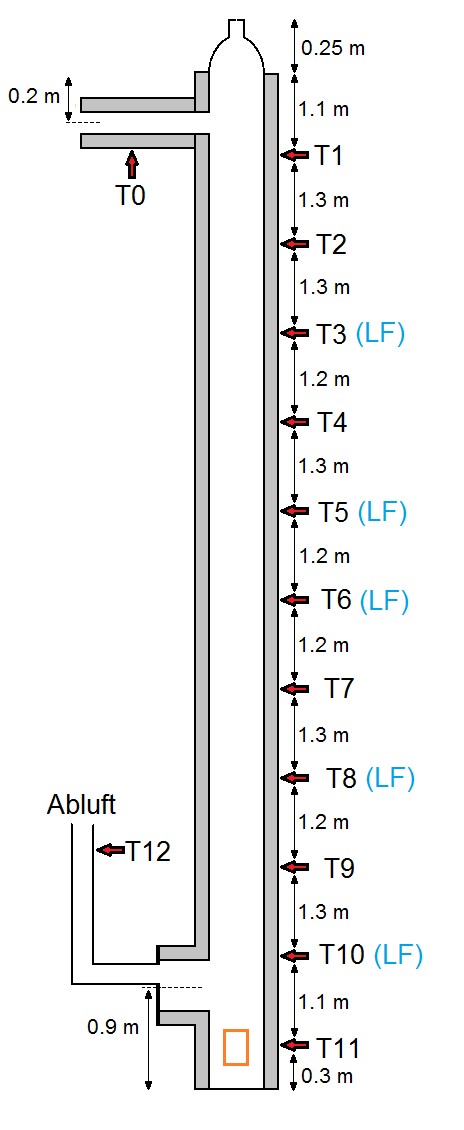
Levitation can be used as a model test for (reactive) spray drying since the floating droplet thus observed behaves in a comparable way to the falling droplets in the spray tower.
Turm 1 | Turm 2 | Turm 3 | |
Total height | 3 m | 6 m | 14 m |
Diameter | 17 cm | 12 cm (volume 68 L) | 35 cm (volume 1.35 m3) |
Heating | Electrical heating jacket | Electrical heating jacket | Heated supply air |
Gas flow | Countercurrent | Countercurrent | Direct current |
Online-Measurements | 7 type K thermocouples | 7 type K thermocouples | 5 humidity sensors |
Investigation of single droplets using acoustic levitation
Droplets can be made to float by means of a standing ultrasonic wave. This technique, known as acoustic levitation, allows the examination of droplets with diameters of up to several millimeters without the influence of a carrier or vessel ("containerless processing").
Chemical reactions in floating single droplets are monitored, for example, using Raman spectroscopy or a CCD camera.
Pyrolsys according to the Hamburg process
Pyrolysis describes thermal decomposition in the absence of air. The Hamburg fluidized bed process is based on decomposition in an indirectly heated fluidized bed. Pyrolysis is becoming more and more interesting these days, especially with regard to plastic recycling. Pyrolysis can convert plastics into their monomers and/or petroleum-like components. This represents a significant advantage over other recycling processes since pyrolysis products can be used to produce new plastics that are suitable, for example, for the food industry.
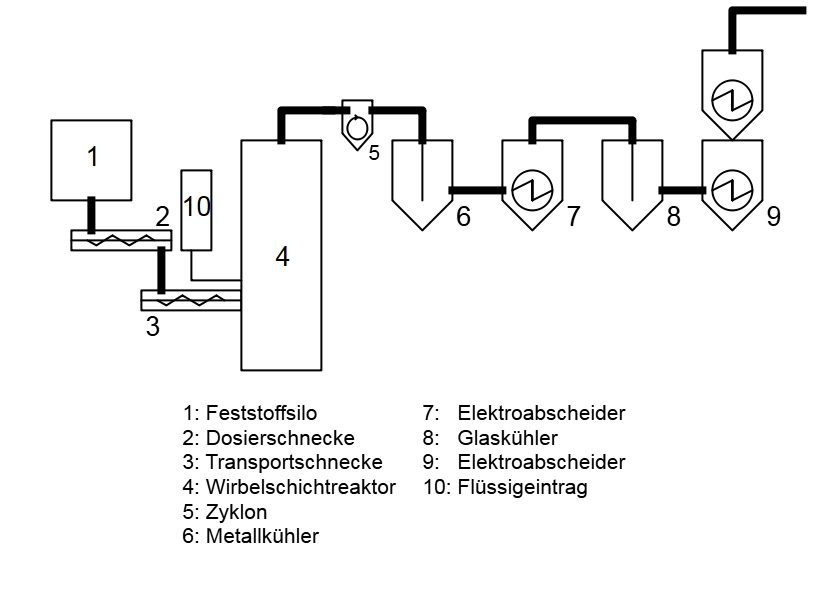
The laboratory fluidized bed reactor can be operated with flow rates in the range of 1 kg / h and at temperatures of up to 700°C. The resulting pyrolysis gas stream is separated into a modular system using cyclones and separators so that different fractions can be examined.